Byrnecut signs up for Sandvik Remote Monitoring Service at 11 sites
Leading contract miner Byrnecut will roll out Sandvik’s Remote Monitoring Service solution at nearly a dozen of its Australian mine sites, following the completion of a successful trial of the technology.
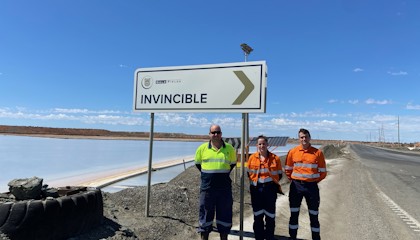
Under a 12-month deal, Sandvik specialists will monitor machine performance and operator behavior on some 95 Sandvik underground trucks and loaders at 11 Byrnecut-operated mines. Daily and weekly reports will help Byrnecut to identify crucial maintenance areas and to encourage best operating practices, with major potential savings and efficiency gains.
“At Byrnecut, we’re serious about continuously increasing productivity, uptime and safety,” said Pat Boniwell, Byrnecut Australia Managing Director. “Based on the results of the three-month trial of Sandvik’s Remote Monitoring Service solution, we are now deploying this technology across all our connected sites in Australia where Sandvik equipment is in use. We’re optimistic that this will yield measurable productivity gains and cost savings for the business.”
Insights into machine and operator performance
Sandvik’s Remote Monitoring Service solution uses the existing technology fitted to the Sandvik equipment to collect telemetry data on an extremely wide range of variables. The data collected is then analyzed by Sandvik data scientists, providing insights into factors such as the health of the engine, transmission, hydraulics, and other machine parts, and how operator behaviors are affecting fuel and parts consumption and efficiency.
Customers receive daily reports on so-called ‘operator violations,’ where Sandvik analysts have detected counterproductive operator behavior. This can include braking and accelerating simultaneously – a practice that prematurely wears out service brakes – running the engine overspeed and selecting inappropriate gears for the conditions at hand.
Weekly reports are delivered on identified maintenance opportunities, such as replacing a part that is rapidly wearing out before it fails and causes an unplanned stoppage to production.
Benefits of OEM expertise
While customers can potentially analyze such data in-house using their own dashboards, using the Sandvik solution means that the data is viewed by OEM experts who understand better than anyone the tolerances of the equipment and common causes for failures and premature wear. In addition to that, Sandvik harnesses large pools of telemetry data for mining equipment. This combination enables us to provide actionable insights in a concise and easy-to-digest form.
Graham Barrow, Sandvik Mining and Rock Solutions’ Business Line Manager – Parts and Services, said the trial of the Sandvik Remote Monitoring Service at an underground gold and copper mine, where Byrnecut provides development and production services for the mine owner, began in July 2022. It ran over three months, during which time Sandvik experts monitored the performance, health and driver behavior on 30 equipment units, including Sandvik LH621i loaders and Sandvik TH663i trucks.
“Byrnecut is always looking to do things better and they identified the mine as a location where they were hoping to increase equipment reliability and maintenance intervals,” Barrow said. “We were very happy to demonstrate how our solution is suited to exactly this task.”
Boniwell said the trial yielded concrete results. “We were able to see a clear reduction in parts costs over the course of the trial, which, of course, is pleasing to us,” he said. “Another key outcome was a change in behavior. As the operators received updates on their performance, they looked for ways to improve and become more efficient. It increased communication between the operators and the maintenance teams and this benefitted the whole operation.”
Operational efficiencies and resource efficiencies are anticipated to contribute to a drop in parts usage and waste, contributing sustainability benefits across the agreement sites.
For more information, please contact:
Graham Barrow
Business Line Manager – Parts and Services
Sandvik Mining and Rock Solutions
graham.barrow@sandvik.com
---------------------------------------------------------------------------
Sandvik Group
Sandvik is a global, high-tech engineering group providing solutions that enhance productivity, profitability and sustainability for the manufacturing, mining and infrastructure industries. We are at the forefront of digitalization and focus on optimizing our customers’ processes. Our world-leading offering includes equipment, tools, services and digital solutions for machining, mining, rock excavation and rock processing. In 2022 the Group had approximately 40,000 employees and revenues of about 112 billion SEK in about 150 countries within continuing operations.
Sandvik Mining and Rock Solutions
Sandvik Mining and Rock Solutions is a business area within the Sandvik Group and a global leading supplier of equipment and tools, parts, service, digital solutions and sustainability-driving technologies for the mining and construction industries. Application areas include rock drilling, rock cutting, loading and hauling, tunneling and quarrying. In 2022, sales were approximately 57 billion SEK with about 16,200 employees.